Manufacturing precision mold tools requires advanced spark methods
Be-Må Molds was founded in 1966 and has been located at its current address, Västbovägen 52 in Värnamo, since 1972. In August 2023, it became part of Nolato AB and simultaneously changed its name to Be-Må Molds AB (formerly Verktygsfirman Be-Må AB).
Be-Må Molds specializes in the design and manufacture of precision mold tools, from prototype tools to multi-cavity tools for medical device components, caps, and closure products in polymeric materials such as plastic, silicone (LSR), and thermoplastic elastomers (TPE).
Our customers are leading companies in the medical technology, pharmaceutical, food, chemical, and cosmetic industries. Our 40 years of experience in LSR tool manufacturing has become one of our specialties, where we extensively use sink and wire EDM.
By being part of the Nolato group and its global teams, Be-Må Molds can offer its old and new customers a complete solution that covers the entire value chain from concept to market. We listen to customer requirements and do our utmost to ensure the project's success. Our vision is to be the customer's first choice as an innovative partner in sustainable development and production.
- "We have over 40 years of experience in manufacturing high-tech mold tools and a recognized reputation for delivering high-quality molds."
- "Our specialty lies in micro to medium-sized products. Our staff is our most valuable asset, and new technology is continuously introduced. By standardizing our systems and processes, we can ensure quality, maximize efficiency, and minimize costs," says Camilla Mårtensson.
- "With world-leading contract manufacturing in Europe, Asia, and North America within the Nolato group, we offer an efficient and highly standardized production platform that enables our customers to optimize logistics, costs, and supply solutions. With certified and environmentally controlled manufacturing facilities worldwide, we are always close to our customers," says Camilla Mårtensson, site manager in Värnamo.
In the photo, we see toolmakers Simon Bolmenius, Branko Brkic, and service technician Auran Industries – Hugo Jansson.
The spark is now an increasingly important problem solver and a green production process.
When you need tight tolerances and a really fine surface, EDM is an excellent method. You can cut almost any shape within the machine's dimensions with very high precision. Customers' components are becoming more designed and complex. Material costs need to be reduced, which results in thinner walled components that need to be manufactured, and there is also a need for EDM.
One of the great advantages of wire EDM machines is that they are very environmentally friendly to work with. You basically only use energy and water, which makes the working environment around the machine good. Operators avoid problems with dust, oil mist, and work in an efficient way that saves material. At the same time, you get production with exact parts that all look the same.
It is possible to cut with a positional accuracy equivalent to a tenth of a human hair, or even better. At the same time, you don't work with tools. You only need wire and electricity. No tools that wear out and need to be replaced.
In the production at Be-Må, we see two different wire EDM machines from SODICK. We ask Roger Jansson to give us technical details about the machines and a bit about EDM in general as an increasingly important player among advanced toolmakers.
- "The Japanese machine builder SODICK is big and strong in the market and experiences that EDM has seen a significant upswing recently because it is an almost indispensable processing method that has developed significantly over the past 25 years. It is, of course, also faster to EDM today, but the big steps have been taken in terms of accuracy and the surfaces we produce using the EDM method."
We start with the wire EDM SODICK ALC400G.
The machine has a working area of 400 x 300 x 220 mm. It can process workpieces up to 860 x 690 x 220 mm with a weight of up to 500 kg. This particular machine is equipped with the following options: Rotary table with both indexing and rotation for EDM of parts at different angles and EDM of, for example, a waist on a test bar. Furthermore, the machine is equipped with linear motors and the 9th generation spark generator.
The next machine we see in production at Be-Må is a SODICK AG40L. Here we get important information about the technology.
- "The linear motor generates an ultra-high speed which creates a pumping effect that effectively removes chips, gas, and carbon that are between the electrode and the workpiece. Therefore, processing can be performed without the need for flushing," says Roger Jansson.
A bit extra about tomorrow's wire EDM;
- "Looking back 30–40 years, there were 10 parts in crack formation, but the finer surfaces we create, the closer the spark can be to the material, the less crack formation we get. Today, we are down to 1000 parts in terms of crack formation. So finally, I can say that we have machines that are now on the market that are so accurate and control the processes so well that we can create a spark surface that you can almost mirror yourself in," concludes Roger Jansson at Auran."
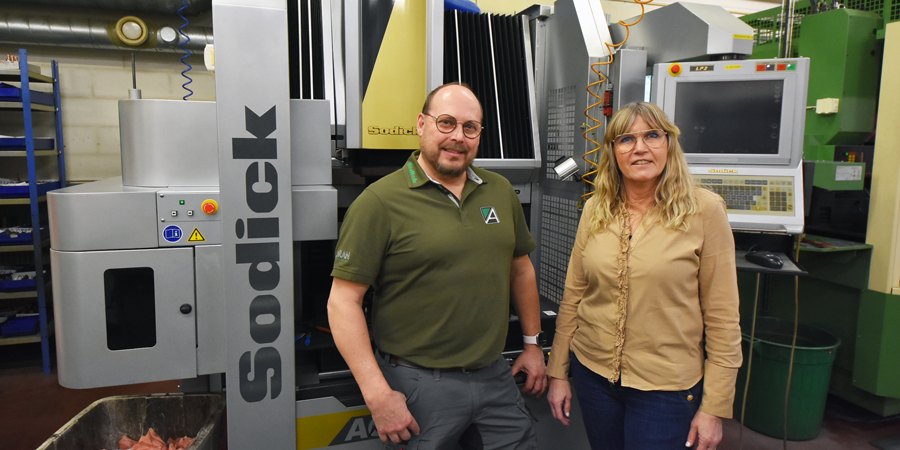
Roger Jansson Auran Industries and Camilla Mårtensson Be-Må Molds.
Article written by the Swedish magasin Maskinoperatören, | NR 8 | Januari 2025