Nine robots team up with reused Swiss machine to produce Husqvarna’s crankcases
Nolato Polymer has been investing heavily in automation in recent years to improve efficiency and competitiveness, while eliminating several monotonous aspects of the workflow.
Most production cells now have one or more robots. The latest addition is the most extensive and advanced production cell to date, and one of the most innovative in the Nolato Group.
Santa’s workshop
Visiting Nolato Polymer’s new production cell in Torekov, where they make components for Husqvarna’s chain saws, is a bit like stepping into Santa’s workshop.
Nine, six-axis robots of various sizes work together in a continual process, which starts with injection molding and ends with labelling the finished article to indicate that it has been approved and is ready for delivery to the customer.
In between these stages, the components are moved from station to station by robots to assemble various inserts and conduct quality checks. For example, at one station the oil tank is welded, while at a subsequent one, pressure testing is carried out to ensure there are no leaks.
Controlled by vision system
Each station is equipped with inspection cameras that both guide and control the process at the station. And instead of shaking out the various subcomponents to be assembled, such as inserts and screws, the robots pick them from a conveyor belt.
The vision system controls the robot, to ensure it only picks the components that are in the right position on the conveyor belt, leaving the others to be picked when they come round again.
The robot also makes sure it has a little buffer stock, from which it can pick a component if it doesn’t find anything on the conveyor belt.
“We’ve been making these kinds of products for Husqvarna for many years, and when we were designing the production process for components for a new model of chain saw, we drew on our experiences with a previous automated cell,” explains Jimmy Wallin, Sales Manager at Nolato Polymer.
“This new production cell is a significant investment, but it’s going to give us a stable process, improved performance, less scrap and extremely high uptime.”
More flexible system
“The robots and the vision systems also make it more flexible. It’s currently programmed to be able to make three different products, and it’s fairly simple to add more,” comments Lennart Thålin, Managing Director of Nolato Polymer.
“It requires fewer man hours; for example, subcomponents are replenished for the various stations in the cell from the outside, which means it can operate without interruption, even when refilling.”
A total of 14 subcomponents are assembled in the production cell before the finished product emerges on the conveyor belt.
Cobots are the future
“Looking ahead there’s scope for further investments in more flexible robots, or ‘cobots’. These are collaborative robots that work alongside humans and are easier to move where they’re needed,” explains Lennart Thålin. “We’re also looking at smarter vision systems that can do things like detect defects in real time.”
The cell also has recycled elements, reflecting Nolato’s focus on sustainability. Instead of installing a new injection molding machine, a used one was relocated from Nolato Treff in Switzerland to Torekov.
“They no longer needed it, so it’s good that we could continue to make use of it,” concludes Jimmy Wallin.
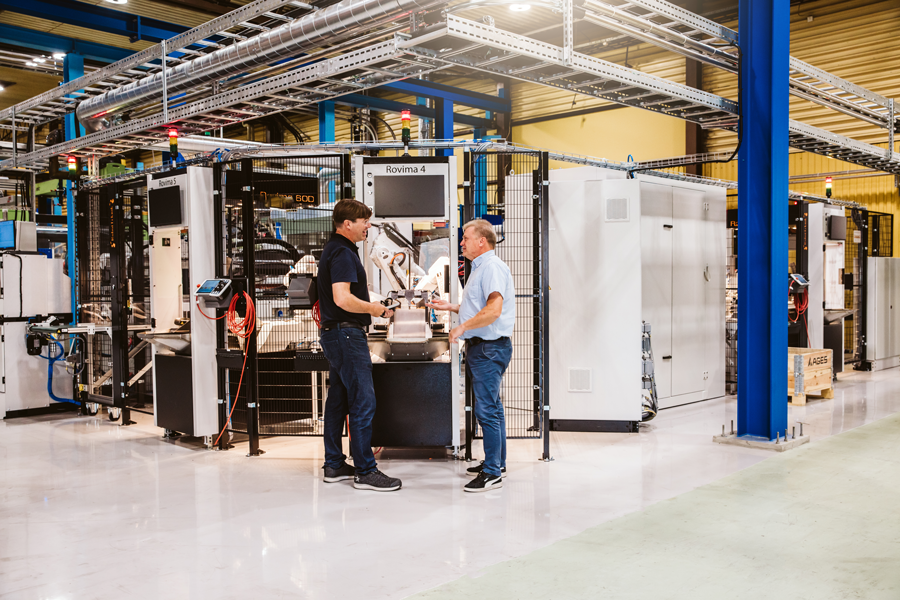
Project manager Fredrik Axelsson and Jimmy Wallin at the new robot cell for Husqvarna.